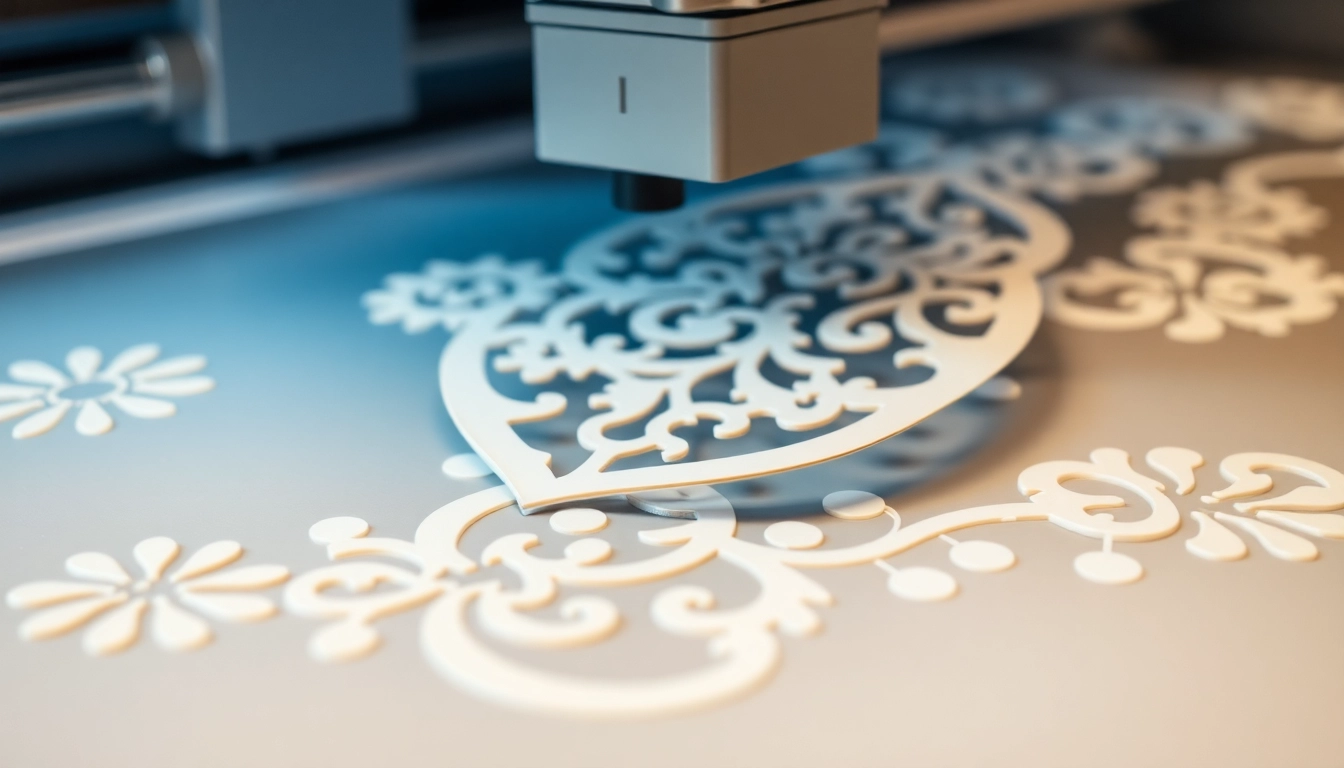
Introduction to Precision Die Cutting
In the ever-evolving landscape of manufacturing and design, precision die cutting has emerged as a cornerstone technology, enabling businesses to produce custom parts and shapes with remarkable accuracy. This technique is integral across various industries, including automotive, aerospace, medical, and consumer goods, where precision and efficiency are paramount. This article aims to provide a comprehensive understanding of precision die cutting, its applications, benefits, and future trends, serving as a guide for businesses seeking to leverage this technology effectively.
What is Precision Die Cutting?
Precision die cutting is a manufacturing process that utilizes a die to cut specific shapes from materials such as paper, plastic, metal, or foam with high accuracy. This technique uses mechanical presses and dies tailored to the unique specifications of the product being manufactured. The precision aspect refers to the ability to produce parts that adhere to stringent tolerances, allowing for consistent quality across production runs. Often, precision die cutting is combined with other processes, like embossing or laminating, to enhance the final product’s functional and aesthetic features.
Applications of Precision Die Cutting
The versatility of precision die cutting makes it applicable in a wide range of sectors:
- Aerospace and Automotive: Used for manufacturing gaskets, seals, and insulation materials that require precise measurements for optimal performance.
- Medical Devices: Vital for producing components like surgical instruments and medical packaging, where precision is crucial for safety and efficacy.
- Consumer Electronics: Essential for creating parts such as decorative overlays, adhesive components, and insulation parts.
- Packaging: Widely used in creating packaging materials that require intricate shapes and designs for branding and functionality.
Advantages of Using Precision Die Cutting Technology
There are several key benefits associated with precision die cutting, making it a preferred choice for manufacturers:
- High Precision and Consistency: The ability to produce uniform parts to exact specifications is crucial for quality control in high-stake industries.
- Efficiency and Speed: Once a die is created, high-speed manufacturing means large volumes can be produced quickly, reducing lead times.
- Cost-Effectiveness: Although the initial setup cost for creating custom dies can be high, the long-term benefits of mass production often lead to lower per-unit costs.
- Material Versatility: This process can handle a wide range of materials, providing flexibility in the types of products that can be manufactured.
Different Types of Precision Die Cutting Techniques
Flatbed Die Cutting Explained
Flatbed die cutting is one of the most common techniques employed in the industry. In this method, a hydraulic flatbed press applies force to a steel rule die to cut material placed on a flat surface. The advantages of flatbed die cutting include:
- Versatility: Ideal for various materials, including thick substrates.
- Cost-Effectiveness for Short Runs: Particularly beneficial for low-volume production where die costs can be amortized.
- Detailed Cuts: Capable of intricate designs, making it suitable for complex shapes.
Rotary Die Cutting: A Closer Look
Rotary die cutting involves the use of cylindrical dies that rotate against the material, cutting it as it moves through the machine. This method is renowned for its speed and efficiency. Key aspects include:
- High Speed: Capable of producing large quantities in a short time frame.
- Continuous Material Processing: Ideal for rolls of material, allowing for seamless cutting without interruptions.
- Precision: Offers tight tolerances and uniform shapes, making it ideal for products requiring exact dimensions.
Laser Die Cutting Advantages and Uses
Laser die cutting utilizes laser technology to cut materials, offering unique benefits:
- High Precision: Lasers can achieve intricate designs that traditional methods may struggle with.
- No Tooling Required: Eliminates the need for physical dies, reducing setup time and costs for small production runs.
- Versatility: Suitable for a variety of materials, including paper, plastic, and thin metals.
Materials Suitable for Precision Die Cutting
Common Materials Used in Precision Die Cutting
A variety of materials can be processed using precision die cutting, including:
- Cardboard and Paper: Often used in packaging and printing industries.
- Foam: Common in medical and automotive applications for gaskets and cushioning.
- Plastic: Utilized in electronic parts and packaging.
- Metal: Thin sheets of metal can be die cut for components in machinery and electronic devices.
Choosing the Right Material for Your Project
Selecting the appropriate material is critical to the success of a die cutting project. Considerations should include:
- End Use: Understand the physical and chemical conditions the part will face.
- Compatibility: Ensure the material can be effectively cut using the chosen die cutting method.
- Cost: Evaluate the cost-effectiveness of different materials against production needs.
Impact of Material Thickness on Precision Die Cutting
Material thickness is a vital factor in die cutting that affects precision and the overall quality of the final product. Key considerations include:
- Tolerance Levels: Thicker materials may require more advanced die designs to achieve tight tolerances.
- Die Wear: Thicker inputs can lead to more wear on dies, impacting production efficiency.
- Cost Implications: Generally, thicker materials are costlier, influencing the overall budget of die cutting projects.
Factors Influencing Precision in Die Cutting
Understanding Tolerances in Die Cutting
Tolerances are a critical aspect of precision die cutting that defines the acceptable variance from specified dimensions. Typical tolerances can range:
- ± 0.005 inches for steel rule dies, especially in short-run productions.
- ± 0.010 to ± 0.015 inches for thicker materials or more complex parts.
Understanding and setting these tolerances is essential for meeting quality standards in manufacturing.
Design Considerations for High Precision Outputs
A successful die cutting project begins with effective design. Considerations include:
- Material Selection: Match the design requirements with appropriate materials.
- Die Design: Ensure that the die allows for clean cuts and minimizes material shrinkage or expansion.
- Prototype Testing: Develop prototypes to validate designs before mass production, allowing refinements if necessary.
Cost Management in Precision Die Cutting Projects
Managing costs is essential in any manufacturing process. For precision die cutting, consider these strategies:
- Batch Size: Optimizing batch sizes can help spread the initial setup costs over more units.
- Material Efficiency: Design layouts that minimize waste during the cutting process.
- Supplier Relationships: Building strong relationships with suppliers can lead to discounts and better pricing on materials and dies.
Future Trends in Precision Die Cutting
Technological Innovations in Die Cutting
The future of precision die cutting is bright, driven by technological advancements. Innovations include:
- Integration of CAD and CAM: Enhanced software tools for more accurate designs and efficient manufacturing processes.
- 3D Printing Technology: The potential to create complex dies with additive manufacturing for reduced lead times.
- Smart Die Cutting Machines: Implementation of AI and IoT for predictive maintenance and enhanced operational efficiency.
The Role of Automation in Precision Die Cutting
Automation is transforming die cutting, promoting efficiency and reducing costs. As robotics and automated systems become more prevalent, benefits include:
- Increased Production Rates: Machines can operate continuously, significantly boosting output.
- Consistency in Quality: Automated systems help reduce human error, ensuring higher quality standards.
- Labor Reduction: Reducing the need for manual intervention allows companies to allocate resources to higher-value tasks.
Sustainable Practices in Precision Die Cutting
Sustainability is becoming a key consideration in manufacturing processes, including die cutting. Companies are pursuing goals such as:
- Reducing Waste: Implementing designs that maximize material usage and minimize scrap.
- Utilizing Eco-Friendly Materials: Sourcing recyclable or biodegradable materials to lessen environmental impact.
- Energy-Efficient Machinery: Investing in machines that consume less energy while maintaining high performance.