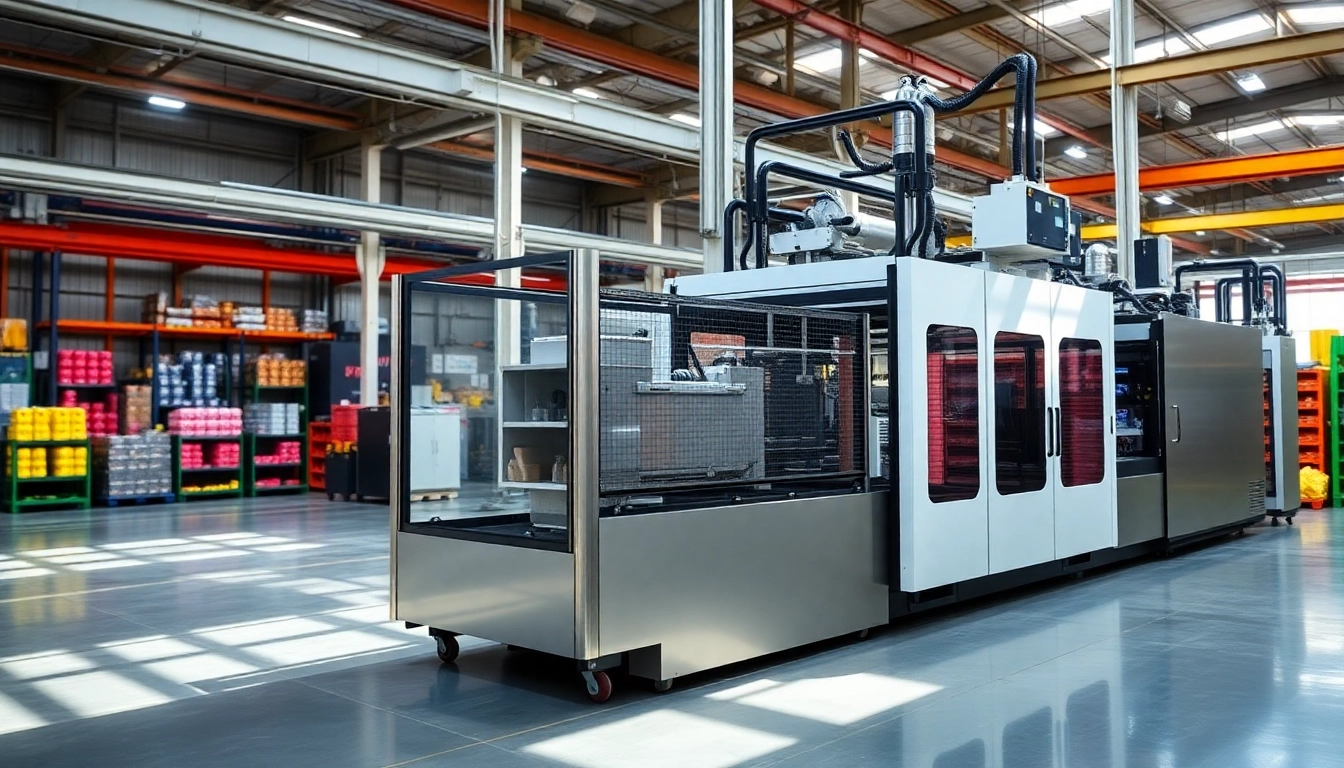
Understanding Blow Molding Technology
What is Blow Molding?
Blow molding is a manufacturing process used primarily for creating hollow plastic parts. The technology emerged in the mid-20th century and has since revolutionized the way containers, bottles, and other hollow objects are produced. The blow molding technique enables high production rates, cost efficiency, and the ability to produce complex shapes with relatively low material wastage. The process involves heating plastic until it becomes pliable, then using air pressure to shape it into a desired form, often within a mold. Companies seeking to invest in production solutions often look to reputable Blow Molding Machine Manufacturers to find machinery that meets their specifications for quality and performance.
Types of Blow Molding Processes
There are three primary types of blow molding processes: Extrusion Blow Molding (EBM), Injection Blow Molding (IBM), and Stretch Blow Molding (SBM). Each method has unique characteristics suited for different applications:
- Extrusion Blow Molding (EBM): This process begins with the extrusion of a tubular parison, which is subsequently inflated into a mold. It’s ideal for larger, simple shapes and is widely used for manufacturing bottles, containers, and tank components.
- Injection Blow Molding (IBM): Here, the production starts with injecting plastic into a mold to form a preform, which is then blown into its final shape. This method offers higher precision and is often used for smaller, complex containers.
- Stretch Blow Molding (SBM): SBM is a variation of injection molding that provides greater strength to the final product. It involves stretching the preform lengthwise and then inflating it to the mold shape, which is particularly popular for producing PET bottles.
Applications of Blow Molding Machines
Blow molding machines are versatile and find applications across various industries, including:
- Packaging: The packaging industry heavily relies on blow molding for creating bottles, jars, and containers for food, beverages, and household products.
- Automotive: Manufacturers utilize blow molding for producing parts like fuel tanks and dashboard components, thanks to their durability and lightweight characteristics.
- Consumer Goods: Products such as toys, sports equipment, and even furniture are made using blow molding techniques, showcasing the process’s flexibility in producing diverse shapes and sizes.
Choosing the Right Blow Molding Machine
Factors to Consider
Selecting the right blow molding machine is pivotal for operational efficiency and product quality. Critical factors to consider include:
- Production Volume: Understanding the required output is crucial. High-speed machines are ideal for bulk production, while smaller units may suffice for low-volume needs.
- Material Compatibility: Not all machines handle every type of plastic equally well. Assessing the material you will use is vital.
- Machine Size and Footprint: Consider the available space in your facility and the machine’s dimensions to avoid issues during installation.
Comparing Machine Specifications
When comparing blow molding machines, examining specifications is key. Some essential metrics to look out for include:
- Clamping Force: The amount of force applied to the mold. Higher clamping forces are necessary for larger products.
- Blow Pressure: This affects the consistency of the end product’s thickness and shape.
- Cycle Time: Shorter cycle times can lead to increased production rates, which can significantly improve profitability.
Manufacturer Reputation and Support
Choosing a blow molding machine manufacturer with a strong reputation in the industry is crucial. Look for:
- Customer Support: Reliable customer service and support for troubleshooting and maintenance can save you time and money.
- Warranty and Repair Services: A comprehensive warranty can protect your investment, and efficient repair services will minimize downtime.
- Industry Experience: Manufacturers with long-standing industry presence often provide superior products owing to their established expertise.
Benefits of High-Quality Blow Molding Machines
Enhanced Efficiency
High-quality machines are engineered for optimal efficiency, reducing production costs and lead times. Advanced technology, such as automation and precision molding, contributes to faster cycle times, allowing for increased output without sacrificing quality. Furthermore, modern machines often come equipped with energy-saving features that decrease operational costs.
Cost-Effectiveness
Investing in a high-quality blow molding machine may initially seem costly; however, the long-term savings are significant. Durable machines tend to require less maintenance, decreasing operational downtime and repair costs. Additionally, high-quality machines can often process a broader range of materials, reducing waste and contributing to cost savings as well.
Product Durability
Durability is a significant benefit of investing in quality blow molding machines. Products manufactured using reliable machines are generally more robust, meeting safety standards and providing customers with long-lasting solutions. This attention to quality typically translates into less product return and warranty claims, ultimately enhancing brand reputation.
Industry Trends and Innovations
Emerging Technologies in Blow Molding
The blow molding industry is continuously advancing through innovations and technological advancements. Key trends involve:
- Smart Manufacturing: Integration of IoT (Internet of Things) systems allows real-time monitoring and predictive maintenance, enhancing machine performance and reducing downtimes.
- 4D Printing: Materials that can change shape over time are emerging, offering new applications for blow-molded products, especially in packaging design.
- Robotics Integration: The use of robotics in the blow molding process streamlines production lines and enhances safety by taking over repetitive and hazardous tasks.
Sustainability in the Blow Molding Industry
Sustainability has reached a crucial tipping point across manufacturing industries, and blow molding is no exception. Companies are now focusing on:
- Recyclable Materials: Shift towards using biodegradable and recyclable plastics is pivotal to meeting environmental regulations and consumer demands.
- Energy Efficiency: Newer machines are designed for energy efficiency, which not only supports budgetary constraints but also reduces carbon footprints through lower energy consumption.
- Less Waste: Innovations in blow molding processes are leading to minimized scrap material, optimizing material use while maintaining product quality.
Future Growth and Market Insights
The blow molding machine market is poised for significant growth, driven by increased demand for sustainable packaging and extensive applications in industries like healthcare and consumer goods. Market research indicates a compound annual growth rate (CAGR) of over 5% in the coming years, fueled by technological improvements in machine efficiency and product capabilities.
Top Blow Molding Machine Manufacturers in the Market
Industry Leaders Overview
Several prominent manufacturers dominate the blow molding machinery landscape, each offering unique advantages:
- Uniloy: A distinguished name in the industry, known for its diverse technology offerings, providing advanced blow molding solutions along with blow molds and related tooling.
- Wilmington Machinery: Specializes in high-speed rotary extrusion blow molding, setting benchmarks in production capabilities.
- Jomar Corporation: Celebrated for its injection blow molding (IBM) machines, emphasizing innovation and reliability.
- Bekum Maschinenfabrik: With a successful H-series of blow-molding machines, it remains a leading force in North America.
- Magic North America: Combines service and cutting-edge technology for comprehensive blow molding solutions, emphasizing Industry 4.0.
Comparative Analysis of Manufacturers
When comparing blow molding machine manufacturers, performance metrics such as energy efficiency, maintenance needs, and customer reviews play significant roles. It is advisable to conduct bench comparisons of machine specifications, features, and overall compatibility with specific production needs. Additionally, reach out to existing clients of manufacturers to gain insights into their experiences regarding support and product performance.
Customer Testimonials and Case Studies
Real-world case studies and testimonials can provide invaluable insight into the performance and reliability of different blow molding machines. For instance, a case study involving Wilmington Machinery illustrates how one client was able to double their production rates while significantly reducing waste through the adoption of advanced blow molding technology. Testimonials frequently cite enhanced efficiency, reduced operational costs, and improved product quality as key benefits of choosing reputable manufacturers in this sector.