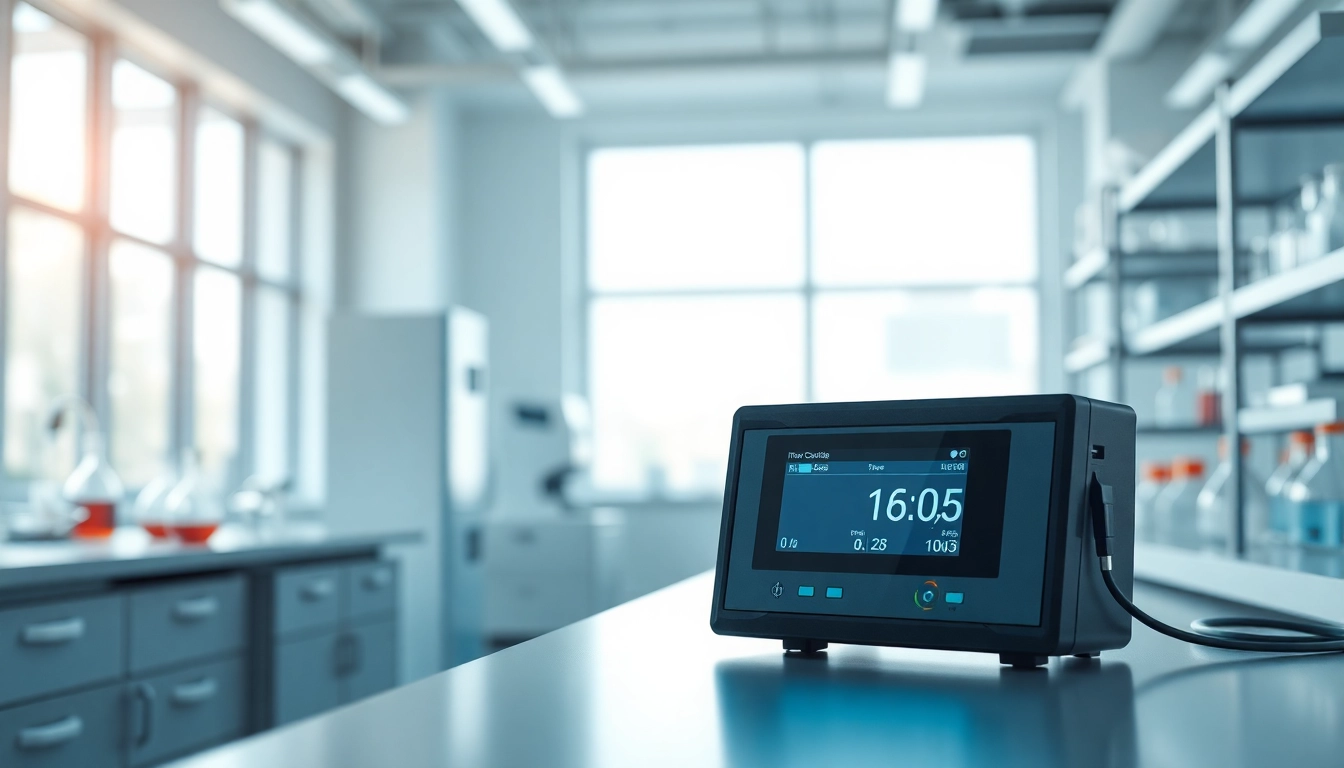
Introduction to Hydrogen Chloride Monitors
Hydrogen chloride (HCl) is a colorless gas known for its pungent smell and corrosive characteristics. It is widely used across various industries, including manufacturing and waste treatment, making monitoring its levels critical for ensuring workplace safety and environmental compliance. Utilizing a Hydrogen Chloride monitor not only safeguards health but also helps in preventing industrial accidents. This article delves into the various facets of hydrogen chloride monitors, outlining their importance, features, selection criteria, best practices, and future trends in technology.
What are Hydrogen Chloride Monitors?
Hydrogen chloride monitors are specialized devices designed to detect and measure the concentration of hydrogen chloride gas in the environment. They provide real-time data to ensure that HCl levels remain within the safety limits established by regulatory authorities. Various types of sensors are utilized in these monitors, including electrochemical cells, infrared sensors, and metal oxide semiconductor sensors, each offering distinct advantages depending on the application.
The Importance of Monitoring Hydrogen Chloride
Monitoring hydrogen chloride is crucial for several reasons:
- Health and Safety: Exposure to HCl can lead to severe respiratory issues, skin burns, and other health complications. Continuous monitoring ensures that workers are safeguarded from harmful exposure.
- Regulatory Compliance: Many industries are subject to stringent environmental regulations regarding HCl emissions. Regular monitoring helps organizations stay compliant, thus avoiding legal penalties.
- Environmental Protection: By monitoring HCl levels, companies can implement timely interventions to prevent environmental contamination.
Common Applications in Industry
Hydrogen chloride monitors are employed in various industries:
- Chemical Manufacturing: Used during the production of chlorinated compounds, petrochemicals, and other related chemicals.
- Waste Treatment: Critical in monitoring HCl emissions from waste incineration facilities and treatment plants.
- Oil and Gas: Essential for detecting leaks in refineries, where HCl can be generated during processing.
Key Features of Effective Hydrogen Chloride Monitors
When considering a hydrogen chloride monitor, several critical features should be evaluated to ensure effectiveness.
Accuracy and Sensitivity Levels
One of the foremost characteristics of a reliable hydrogen chloride monitor is its accuracy and sensitivity. Monitors should provide precise readings even at low concentrations of HCl. Advanced devices can detect HCl levels in the parts per million (ppm) range, ensuring that minute fluctuations are identified promptly.
Durability and Environmental Considerations
Given the harsh environments in which hydrogen chloride monitors often operate—such as chemical plants and manufacturing sites—durability is key. Units should offer protection against corrosive elements, moisture, and extreme temperatures. Many effective monitors have rugged designs and are made from durable materials that withstand harsh conditions.
User Interface and Data Presentation
A user-friendly interface is essential for effective operation. The display should provide clear, immediate readings of hydrogen chloride levels without complicated navigation. Additionally, advanced models may offer data logging, allowing users to track changes over time and generate reports for compliance and safety reviews.
How to Choose the Right Hydrogen Chloride Monitor
Selecting the appropriate hydrogen chloride monitor can significantly influence workplace safety and compliance. Here are key factors to consider.
Factors to Consider in Selection
- Application Needs: Assess the environment in which the monitor will be used, including potential interference from other gases and the typical concentration ranges of HCl.
- Calibration Requirements: Understand the calibration process for the device. Many monitors require regular calibration for optimal accuracy.
- Portability: Depending on usage, consider whether a portable or fixed monitor best meets your needs.
Comparison of Leading Brands
Several manufacturers specialize in hydrogen chloride monitoring, each offering devices with unique features and specifications. It’s beneficial to compare product reviews, user experiences, and technical support options. For instance, some well-known brands may offer advanced sensor technologies, while others might focus on affordability.
Cost vs. Quality Considerations
While price is always a consideration, investing in a high-quality hydrogen chloride monitor can yield better long-term benefits. Consider the cost of ownership, including maintenance and potential liabilities associated with sensor inaccuracies or failures. Balancing initial costs with reliability and performance can lead to wise purchasing decisions.
Best Practices for Using Hydrogen Chloride Monitors
Implementing best practices ensures that hydrogen chloride monitors function effectively and maximize safety benefits.
Regular Calibration and Maintenance
Regular calibration is essential to maintain the accuracy of hydrogen chloride monitors. Calibration checks should be performed according to the manufacturer’s guidelines, usually on a monthly or quarterly basis. Additionally, routine maintenance, such as sensor cleanings and battery checks, ensures optimal functionality.
Training Staff for Effective Monitoring
Employees should undergo comprehensive training regarding the operation of hydrogen chloride monitors. Training should cover proper usage, potential hazards, and emergency response protocols to ensure your team is prepared for any situation.
Interpreting Readings and Data Management
Understanding and interpreting the readings from hydrogen chloride monitors is vital for effective safety implementation. Regular reviews of data logs can help identify trends and potential issues before they become significant problems. Integration with data management systems can facilitate analysis, reporting, and compliance documentation.
Future Trends in Hydrogen Chloride Monitoring Technology
The field of hydrogen chloride monitoring is evolving rapidly, propelled by advancements in technology and regulatory changes.
Advancements in Sensor Technology
Emerging sensor technologies are enhancing the accuracy, responsiveness, and longevity of hydrogen chloride monitors. Innovations such as nanotechnology-based sensors promise to deliver faster and more precise readings with improved resistance to environmental conditions.
Integration with Smart Systems
Smart monitoring systems that connect with other safety technologies are gaining traction. These integrated systems can provide comprehensive safety solutions and facilitate real-time data sharing across organizational platforms, enhancing overall safety management.
Regulatory Changes and Industry Impact
Regulatory agencies continue to update standards and guidelines regarding hazardous gas monitoring. Staying informed about changes can impact compliance strategies, as organizations must adapt their monitoring protocols accordingly to adhere to new regulations.
In conclusion, hydrogen chloride monitoring is essential for health and safety across various industries. Understanding the features of hydrogen chloride monitors, how to choose the right one, and best practices for usage can significantly enhance workplace safety. The continual advancements in technology promise even greater efficiency and effectiveness in monitoring, ensuring that organizations can maintain compliance and protect their workers.