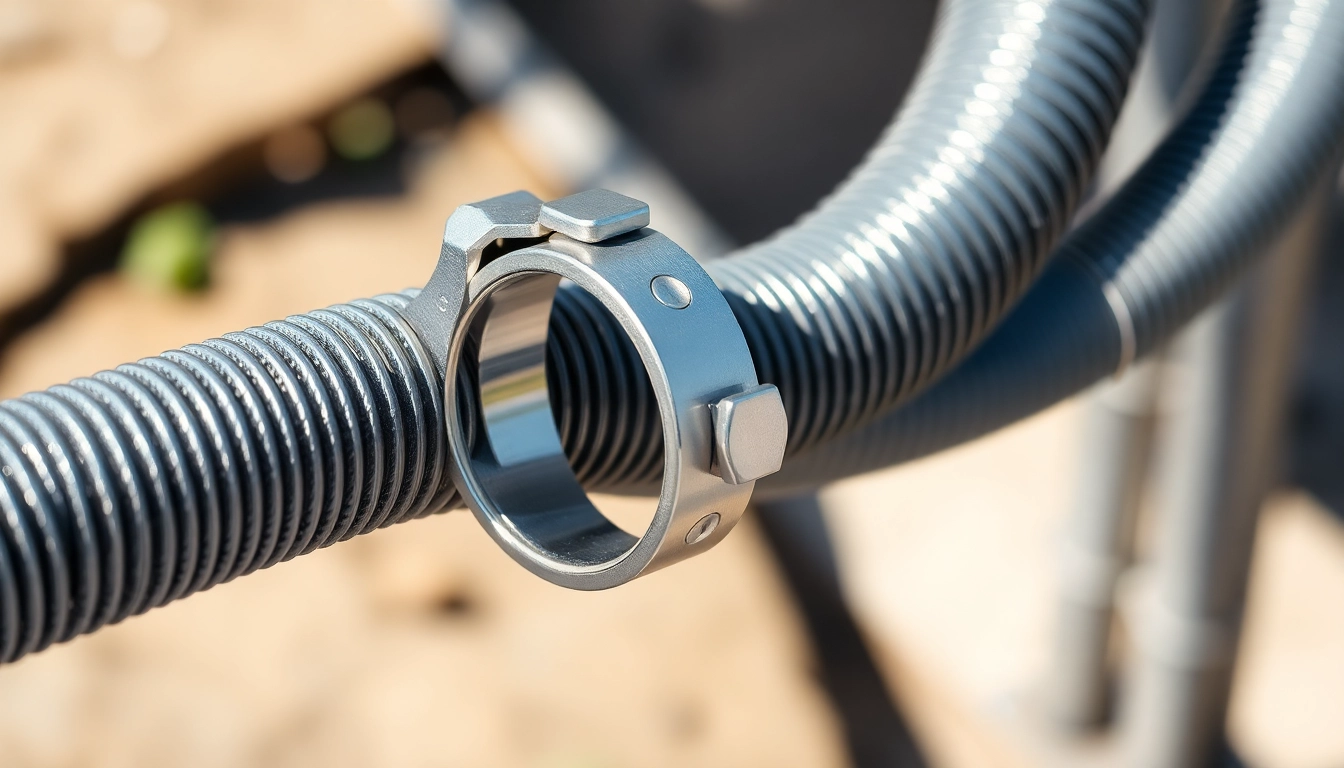
Understanding the Basics of Clamp on Hose Applications
Clamp on hoses are essential devices in various industries, enabling seamless connections, fluid management, and equipment functionality. By securely holding hoses in place, these clamps prevent leaks and ensure efficient operation. Whether you are working in automotive, plumbing, or industrial settings, understanding the intricacies of clamp on hose applications is crucial. This article aims to enlighten readers about the fundamentals, types, selection criteria, installation processes, and maintenance practices associated with clamp on hoses.
What is a Clamp on Hose?
A clamp on hose typically refers to a hose fitting method where the hose is attached to a coupling or fitting using a clamp, which secures it in place. The clamp applies constant pressure around the hose, preventing disconnections and leaks. These hoses are often used in applications where fluid, air, or other materials need to be transported safely. Depending on the type of clamp used, the connection can be permanent or temporary, making it a versatile solution for various industries.
Common Uses for Clamp on Hoses
Clamp on hoses find application across many industries due to their reliability and ease of use. Common uses include:
- Automotive: Used to connect fuel, coolant, and air intake hoses, ensuring optimal engine performance and safety.
- Plumbing: Essential for securing water supply lines, drain lines, and irrigation systems, preventing leaks and water damage.
- Industrial Manufacturing: Utilized in machinery and assembly lines to handle various fluids, ensuring efficiency and safety in operations.
- Aerospace: Employed in fuel systems and hydraulic systems where secure connections are imperative.
Benefits of Using Clamp on Hoses
The advantages of clamp on hoses stem from their design and utility:
- Ease of Installation: They can be installed quickly with minimal tools, allowing for efficient repairs and replacements.
- Leak Prevention: When installed correctly, clamp on hoses effectively prevent leaks, reducing downtime and material waste.
- Versatility: Available in various sizes and materials, they can adapt to multiple applications.
- Cost-Effective: Their simple mechanism reduces overall maintenance costs and extends the life of hoses by preventing damage.
Types of Clamp on Hoses Available
Clamp on hoses come in various designs, each tailored to meet specific application needs. Understanding these types can help determine the best option for your requirements.
Worm Gear Clamp on Hoses
Worm gear clamps are one of the most commonly used hose clamp types. They consist of a band with a threaded screw that tightens the band around the hose. The benefits of worm gear clamps include:
- Adjustability: Easily adjustable to accommodate different hose sizes.
- Durability: Typically made from stainless steel, they are resistant to corrosion and wear.
- Strong Sealing: Provides a reliable and secure connection, suitable for high-pressure applications.
Spring Clamp on Hoses
Spring clamps use a spring mechanism to apply pressure to the hose, making them ideal for applications where the hose may expand or contract. Advantages include:
- Dynamic Fit: Adjusts automatically to changes in hose size due to temperature fluctuations.
- Simple Installation: Can be easily installed and removed without any tools.
- Lightweight: They add minimal weight to the assembly, making them suitable for aerospace applications.
T-Bolt Clamp on Hoses
T-bolt clamps feature a T-bolt mechanism providing excellent torque and a strong grip, ideal for heavy-duty applications. Key attributes include:
- High Pressure: Suitable for high-pressure applications due to their robust design.
- 360-Degree Coverage: Ensures complete clamping around the hose, preventing leaks.
- Reusability: Can be tightened or loosened multiple times without losing effectiveness.
How to Choose the Right Clamp on Hose
Choosing the correct clamp on hose is crucial for ensuring effective performance and safety. Consider the following factors when making your selection:
Assessing the Application Requirements
Identifying the specific needs of your application is essential. Consider the following:
- Fluid Type: Ensure the clamp material is compatible with the fluid being transported.
- Pressure Requirements: Assess the pressure and temperature to choose a clamp that can withstand those conditions.
- Environment: Evaluate whether the hose will be exposed to chemicals, abrasives, or other harsh conditions.
Material Considerations for Performance
The material of both the hose and the clamp plays a significant role in performance. Common materials include:
- Stainless Steel: Offers excellent corrosion resistance and durability.
- Plastic: Lightweight and resistant to rust, often used in less demanding environments.
- Aluminum: Lightweight with good corrosion resistance but less robust than stainless steel.
Size and Compatibility Factors
Ensuring that the hose clamp fits properly is vital. Measure the diameter of the hose and consider:
- Clamp Size: Choose a clamp that securely fits around the hose without excessive slack.
- Hose Thickness: Ensure the clamp accommodates the wall thickness of the hose material.
- Fitting Compatibility: Ensure the clamp can attach to the specific fittings being used.
Installation Tips for Clamp on Hoses
Proper installation is crucial for the effective performance of clamp on hoses. Here are essential tips for successful installation:
Tools You’ll Need for Installation
Having the right tools at hand can significantly speed up the installation process:
- Hose cutter or sharp utility knife for precise hose cutting.
- Wrenches or screwdrivers (depending on the type of clamp) for tightening the clamps securely.
- Measuring tape to ensure proper hose length and fittings.
Step-by-Step Installation Guide
Follow these steps for proper installation of clamp on hoses:
- Measure and Cut: Measure the required length of the hose and cut it with a hose cutter.
- Prepare the Fitting: Ensure that the fitting surface is clean and free of any debris.
- Slide the Clamp: Slide the clamp onto the hose before connecting it to the fitting.
- Attach the Hose: Push the hose onto the fitting, making sure it fits snugly.
- Tighten the Clamp: Use the appropriate tool to tighten the clamp securely and evenly around the hose.
Common Mistakes to Avoid
To ensure a successful installation, avoid these common mistakes:
- Over-tightening: This can damage the hose or fitting, leading to leaks.
- Incorrect Clamp Size: Using the wrong size can lead to insecure connections and potential leaks.
- Debris in Fitting: Always clear the connection area to ensure a proper seal.
Maintaining and Troubleshooting Clamp on Hoses
Routine maintenance and troubleshooting are key to extending the lifespan of clamp on hoses. Here are best practices:
Regular Maintenance Best Practices
To keep clamp on hoses functioning optimally, implement these maintenance practices:
- Visual Inspections: Regularly inspect for signs of wear, leaks, or damage.
- Tightness Checks: Periodically check the tightness of the clamps to ensure they are secure.
- Cleanliness: Ensure the hoses and fittings are clean and free of contaminants.
Identifying and Fixing Common Issues
If you encounter issues with clamp on hoses, consider the following troubleshooting steps:
- Leak Detection: If you notice leaks, check the tightness of the clamps and inspect the hose for damage.
- Wear and Tear: Replace hoses that show signs of severe wear or cracking.
- Material Weakness: If a clamp is rusty or corroded, replace it immediately to prevent failures.
When to Replace Your Clamp on Hose
Recognizing when to replace hoses is crucial for safety and efficiency:
- Visible signs of wear or cracking on the hose.
- Frequent leaks despite attempting to tighten clamps.
- Changes in performance, such as decreased flow rate or pressure drop.